What is the immersion burner installed in the zinc pot
2025-04-22 11:06:43
Immersion burners (also known as submerged combustion burners) are high-efficiency combustion devices specifically designed for heating zinc pots in galvanizing production lines. They are installed directly inside the molten zinc for heating.
Basic Working Principle
Direct Contact Heating: The burner is immersed in the zinc bath, with combustion gases directly transferring heat to the molten zinc.
Forced Convection: High-speed gas ejection creates intense agitation in the zinc bath, enhancing heat transfer efficiency.
Fully Submerged Combustion: The combustion process occurs entirely within the zinc bath, with no exposed flames.
Key Structural Features
Corrosion-Resistant Combustion Tube: Typically made of 310S stainless steel or special alloys to resist zinc corrosion.
Porous Design: The burner head features a multi-hole structure to evenly disperse combustion gases.
Cooling System: Some designs include water-cooled jackets to protect the burner from high-temperature zinc damage.
Special Sealing: Prevents zinc infiltration into the combustion system.
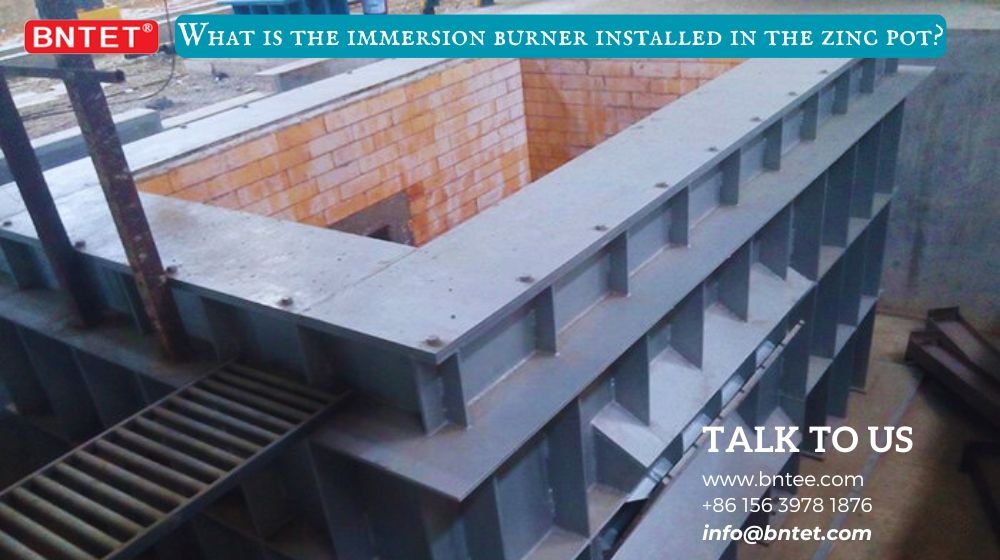
Performance Advantages
Exceptionally High Thermal Efficiency (90-95%):
- Direct heat transfer.
- Nearly all waste heat is absorbed by the zinc bath.
Rapid Heating:
- 3-5 times faster than traditional external heating methods.
- Reduces production line startup time.
Uniform Temperature Distribution:
- Gas agitation ensures even zinc bath temperature (±1-2°C).
- Minimizes localized overheating and zinc dross formation.
Significant Energy Savings:
- 30-50% more efficient than radiant tube heating.
- Exhaust gas temperature is only 10-20°C higher than the zinc bath.
Special Design Requirements
Anti-Zinc Backflow: Must include safety devices to prevent zinc backflow.
Thermal Shock Resistance: Capable of withstanding frequent start-stop thermal cycles.
Ease of Maintenance: Designed for regular cleaning of zinc ash deposits.
Flame Monitoring: Equipped with a reliable flame detection system.
Application Considerations
Installation Position: Typically located on the sidewall or bottom of the zinc pot, avoiding workpiece travel paths.
Supporting Systems: Requires precise gas/air ratio control systems.
Zinc Bath Cleanliness: Regular removal of zinc dross buildup on the burner surface.
Safety Interlocks: Must be linked to zinc level monitoring to prevent low-level operation.
This type of burner is particularly suitable for large-scale continuous galvanizing lines but demands professional design and strict operational maintenance protocols.